When Food Safety Goes Wrong: Legal Ramifications for Companies
- Emily
- Oct 4, 2024
- 5 min read
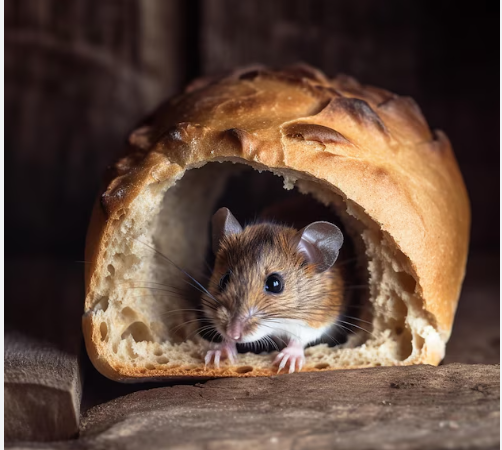
In today’s fast-paced world, where consumers place high trust in the brands they support, food safety is a critical concern for companies and the public alike. A single mistake can lead to outrage, financial loss, and reputational damage that takes years to recover from. This was the reality for Sasko, following a widely shared incident where a rodent was reportedly found in a loaf of bread by consumer Nombulelo Mkumla. This shocking discovery, captured in a viral video on social media, has once again brought food safety standards and legal obligations to the forefront.
In this article, we explore the legal obligations that food producers like Sasko face under South African law, with a particular focus on the Consumer Protection Act (CPA), hygiene regulations, and the serious consequences of failing to meet these standards. We also provide a guide for businesses on how to handle food contamination complaints, ensuring they stay compliant and manage such crises effectively.
Legal Obligations of Food Producers Under South African Law
Consumer Protection Act (CPA): Ensuring Product Safety
Under the Consumer Protection Act, 2008 (CPA), food producers in South Africa have a duty to ensure that their products meet strict safety and quality standards. Section 55 of the CPA guarantees consumers the right to receive goods that are:
Suitable for their intended purpose: This means food products should be safe for consumption, without any health risks from contamination or foreign objects like rodents.
Free from defects: Consumers expect their food to be of acceptable quality—free from any defects, including contamination that would make the food unsafe to eat.
Durable for a reasonable time: Food should remain safe within its shelf life and stored properly to avoid contamination.
The CPA holds companies strictly liable for harm caused by unsafe products, even if no negligence is proven. Section 61 of the CPA establishes this strict liability for:
Supplying unsafe goods
Product defects or failures
Inadequate instructions or warnings about potential hazards
If Sasko is found to have violated hygiene protocols, they could face serious legal consequences, including liability for any harm caused to consumers, from physical illness to emotional distress. Given the viral nature of this incident, reputational damage could lead to significant civil claims, and businesses in the food industry must take incidents like these seriously.
Hygiene Regulations for Food Premises
Beyond the CPA, the Regulations Governing General Hygiene Requirements for Food Premises and the Transportation of Food (GNR.918 of 1999) impose strict hygiene requirements on food producers.
Key obligations include:
Pest control: Food premises must be free of contamination from pests like rodents, which can compromise food safety.
Regular inspections: Food production areas and machinery must be routinely cleaned and sanitized to prevent contamination.
Failure to comply with these hygiene regulations can result in hefty penalties, including business closures, fines, or reputational damage. Sasko’s decision to halt production pending an investigation was a smart move to manage risks. However, if it’s revealed that Sasko failed to comply with hygiene standards, they could face sanctions from health authorities.
Consequences of Non-Compliance
Civil Liability: Compensation and Damages
Under Section 61 of the CPA, consumers harmed by unsafe products can claim compensation for injuries, illness, or damage to property. Even though Mkumla did not physically consume the contaminated bread, the emotional distress from discovering a rodent in her food could lead to a claim for psychological harm. Courts can award damages for emotional trauma, particularly where health risks are involved.
In addition, Section 56 of the CPA allows consumers to return defective goods within six months of purchase, with the right to demand a refund, repair, or replacement. This means Sasko could face multiple compensation claims from other customers during the same production period.
Regulatory Penalties and Product Recalls
If food safety violations are found, regulatory bodies like the National Consumer Commission (NCC) and the Department of Health can impose penalties. Under Section 60 of the CPA, the NCC can also mandate a product recall if there’s evidence that a product poses a risk to public safety. If systemic issues are found in Sasko’s production process, the company may be required to conduct a nationwide recall.
Non-compliance with hygiene regulations under the Health Act, 1977 could result in administrative fines or even facility closures until the company demonstrates compliance.
How to Handle Food Contamination Complaints: A Legal Guide for Businesses
The Sasko incident offers key lessons for all food manufacturers. How a company responds to food contamination complaints is critical to maintaining consumer trust and minimizing legal fallout.
Here’s a guide to best practices for managing such situations.
1. Immediate Investigation and Response
The first step after a contamination complaint is received is to conduct a thorough internal investigation. In Sasko’s case, the company promptly halted production at the affected facility, signalling to the public that it took the matter seriously.
Inspect the facility, identify the source of the contamination, and implement immediate corrective measures. For Sasko, the presence of a rodent suggests a failure in pest control, requiring immediate action to rectify this lapse.
2. Notify Health Authorities
Food producers are legally required to notify health authorities when contamination is detected. According to the Consumer Product Safety Recall Guidelines (GN 490 of 2012), companies must notify the NCC within two days of becoming aware of an unsafe product or initiating a recall. This demonstrates transparency and ensures proper oversight of corrective actions.
By notifying the authorities early, companies show they are taking responsibility and working to resolve the issue in collaboration with public health bodies.
3. Managing Consumer Relations
How a company treats consumers during a food safety crisis can make or break its reputation. While Sasko did offer Mkumla a refund, the company must be careful in its communication to avoid giving misleading information. The assurance she received that the contaminated bread posed no health risk raised additional concerns.
Best practices include:
Offering immediate refunds, replacements, or compensation
Covering any necessary medical expenses
Apologizing sincerely and explaining the corrective steps being taken
Clear, empathetic communication is essential to maintaining consumer trust.
4. Implement Corrective and Preventative Measures
Once the source of contamination is identified, swift corrective action must be taken. In Sasko’s case, this could involve enhancing pest control measures and updating hygiene protocols. Implement preventative measures to avoid future incidents, such as improved monitoring systems and more frequent inspections.
These corrective actions should be communicated to both the consumer and health authorities to demonstrate a commitment to resolving the issue and preventing recurrence.
5. Public Relations and Damage Control
In today’s age of social media, a company’s response to a crisis can spread quickly. Sasko’s public statement highlighted its commitment to safety, but ongoing transparency is key to rebuilding public trust.
A strong public relations strategy should include:
Public apologies and taking responsibility for the mistake
Assurance that corrective actions are being taken to protect consumer safety
Continuous updates to the public on the progress of the investigation
By being transparent and proactive, companies can limit long-term damage to their reputation.
6. Handling Product Recalls
If the contamination extends beyond a single product or batch, a product recall may be necessary. Section 60 of the CPA empowers the NCC to mandate a recall if public safety is at risk.
Best practices for managing a recall include:
Setting up clear collection points for returned products
Communicating the recall process clearly to consumers
Keeping detailed records of the recall to show compliance
Though recalls can be damaging, they also provide an opportunity for companies to demonstrate their commitment to consumer safety.
Conclusion
The Sasko incident serves as a stark reminder of the importance of maintaining high food safety standards. Food producers in South Africa are bound by strict regulations under the CPA and hygiene laws, and when those standards are not met, the legal and reputational consequences can be severe.
However, by acting swiftly, notifying health authorities, addressing consumer complaints with care, and taking corrective measures, companies can mitigate the fallout. In the age of viral social media, transparency and prompt action are the best defences against long-term reputational damage. Food safety isn’t just about avoiding legal trouble—it’s about building and maintaining consumer trust in your brand.
Comentarios